常州市透明紫外线石英消毒灯定做
发布时间:2024-09-29 00:31:56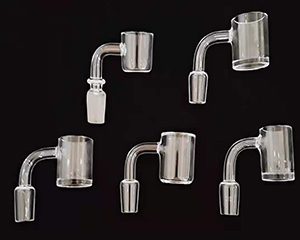
常州市透明紫外线石英消毒灯定做
近些年来,由于我国不断加大对电子信息产业的发展力度,同时也促进了石英玻璃市场需求量的迅速增长。在微电子领域,对消耗性的关键材料石英玻璃扩散管、坩埚、仪器器皿等石英制品的需求正与日俱增。4英寸~8英寸电路用石英扩散管的需求量在“十一五”时期达到了2万支/年;8英寸~12英寸也大幅度增加。石英坩埚按生产硅单晶的级别分为电子级和太阳能级。2004年硅单晶产量为1725吨,太阳能电池硅单晶约占58%,市场年增长率为27.5%,坩埚的年产量已超过10万只,市场占有率不断提高。国内光纤市场以每年12%速度递增。2004年沉积管和套管的需求量为300吨,国内仅能生产20吨。我国电光源石英玻璃生产企业已有40多家,拥有连熔炉近100多台,“十一五”期间的市场平均增长率在20%左右,石英管的总产量约53500吨。
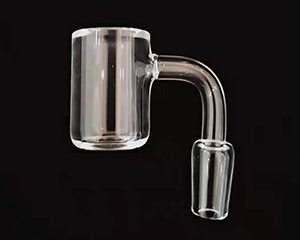
常州市透明紫外线石英消毒灯定做
快盈lll平台(1)检测石英管的阻值:石英管可以通过万用表检测其阻值,将万用表挡位调至“蜂鸣挡”,将红黑表笔分别搭在石英管的两端,此时万用表的蜂鸣器应当发出响声,并且指针应当指向零。若检测时,万用表蜂鸣器无声音发出,并且指针指向无穷大时,说明石英管的内部发生损坏。(2)检测石英管的供电电压:检测石英管的供电电压时,首先将万用表的量程调至“交流250V”电压挡,红黑表笔分别搭在石英管的供电端。此时观察万用表的读数,若在交流220V左右,则说明石英管的供电电压正常。
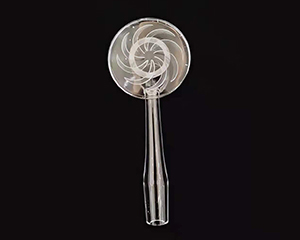
常州市透明紫外线石英消毒灯定做
快盈lll平台如果采用多晶硅和石英玻璃的联合制备法,由还原炉里出来没有参加反应的还原料不进入回收系统,而被当成生产石英玻璃的原料直接进入制砣机,因此不用降温。也就是说,采用多晶硅和石英玻璃的联合制备法生产多晶硅是可以避免上述浪费的,可以节约80%~90%的能源。这只是生产多晶硅,采用多晶硅和石英玻璃的联合制备法来生产石英玻璃也一样具有明显的节能优势。采用传统的单项生产法生产石英玻璃,也需要将送进制砣机的合成料加热,而且升温的幅度要更大。一般认为,制砣机的反应区里要达到1400~1600℃的高温,而要达到如此高温需要消耗大量的能源。传统的单项生产法生产石英玻璃是靠氢氧燃烧来获取高温的。我们知道,在单项生产的合成料里已经含有氢气了,可为了达到此高温,还得另外向制砣机的反应区里通人燃料氢气和助燃的氧气,而且燃料氢气的量要大于合成料所含的氢气。如果采用多晶硅和石英玻璃的联合制备法,由还原炉里出来没有参加反应的还原料被当成合成料直接进入制砣机。该料温度已经很高,在1150~1250℃左右。这样的料通入制砣机就不用再另外向制砣机的反应区通人燃料氢气,因为该料所含的氢气燃烧所产生的热量已经完全可以满足化学反应的需要了。由此可以看出,采用多晶硅和石英玻璃的联合制备法来生产石英玻璃可以节省50%~6()%的氢气,可见这些数字是相当可观的。
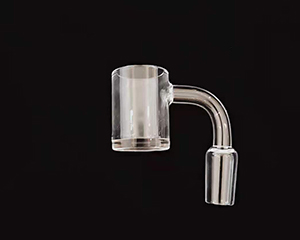
常州市透明紫外线石英消毒灯定做
快盈lll平台多晶硅和石英玻璃的联合制备法的热能是被充分利用的,其生产过程没有反复升降温的现象,因此可以节能,而且节能的数字是相当可观的。采用传统的单项生产法生产多晶硅,还原料从鼓泡器里出来后被送进还原炉。在炉内还原料被加热到1150~1250℃,发生了氢还原反应,生成多晶硅。采用这种生产法,进入还原炉的还原料只有少数(一般认为10%~20%)参加反应,生成了多晶硅,绝大多数被当作尾气排放了。初,这些尾气被当成废气放掉,造成极大的浪费。为避免浪费,人们把尾气中的氢气和四氯化硅回收,经净化提纯后再利用。这样一来,出来的高温料,进入由冷冻分离器和氢气回收组成的回收系统回收。在回收系统里,还原料被冷冻降温至四氯化硅的沸点(57.6。C)之下,一般认为应在40~38℃为好。如按还原料在还原炉里的低限温度1150℃,降温后的上限温度40。C计算,也要降温1100℃。问题是,回收后4()℃的常温还原料要重新被送入鼓泡器里,然后通进还原炉,再次被加热到11501250。C的高温。从上述工艺中可以看出,进入还原炉被加热的大部分还原料(占进炉料9()%)没有被利用就被送出降温,而且降温后又被重新送入还原炉成为参加新一轮反应的还原料。很明显,这是一种浪费,没有参加反应的还原料按理说应该不加热。可问题是,在还原炉里,没有参加反应的还原料与参加反应的还原料是混在一起的,根本无法分开,如果没有参加反应的还原料不加热,那么,参加反应的还原料也无法加热。我们知道,参加反应的还原料温度低是无法进行化学反应的,也就无法生产出多晶硅。所以,如果采用传统的单项生产法生产多晶硅的话,上述浪费是不可避免的。